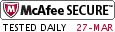
Sunday, May 13, 2012
Friday, April 27, 2012
Construction of Asphalted Surfaces - How to Choose A Contractor
Are you planning to hire a contractor who will take charge of the construction of a drive way, parking lot or a tennis court for you? You need to be prepared to spend good money on this project in order to ensure that the surface that is created lasts very long and does not give you any trouble. However, are you certain that the contractor you are planning to hire is a reliable one? The following tips will help you select one who will do the job for you in the best manner possible.
At the very outset, you need to check whether the construction company has the necessary expertise and equipment to get the job done. Asphalting a surface, even one as short as your driveway, is a complicated job involving various processes. If the contractor is not able to handle the job properly then the surface that is created will not last very long.
At the same time, there is a possibility that well established and popular businesses will not be able to give you the level of attention you require. You should only give your business to a company whose representative takes the time out to understand what your specific needs are and also whether your property has any unique problems. This will ensure that you are offered a solution that matches your needs.
Make sure that you deal with a company that is known for sticking to precise timelines. The last thing you need is a construction crew stationed on your property for days on end. The company you give your contract to should be able to inform you in writing regarding the completion date of the project. You will also get a good idea about a company's level of professionalism from its ability to stick to a schedule. It is also a very good idea to enquire whether the contractor has taken the necessary insurances that will protect you in the event of any accident whilst the work is going on in your property.
Feel free to ask the company for any references of clients for whom it has done work in the past. If the construction company is hesitant about sharing this information then you have every reason to be suspicious about the quality of services it offers. If you choose your contractor based upon these tips then you can be sure that you will be satisfied with the results of its work.
Using A Scaffold Hoist
Builders and scaffolders will most likely know how utilising a scaffold hoist can be advantageous in many ways, if you do not know or wish to know more regarding these hoists then this article provides that information.
So what is a scaffold hoist? It is an electrical device that is used primarily on scaffolding towers to enable the safe and swift lifting and lowering of resources and equipment to practically any height. They clamp securely to any of the scaffolding poles enabling them to be placed just about anywhere they may be needed. Principally seen employed within the construction industry and for roofing purposes, or wherever scaffolding is used. Available devices will vary in the speed of their lifting capability and also the length of wire rope to provide a version to suit nearly all purposes.
Most forms of construction work will require materials to be taken up to a height where they are needed and normally use some kind of scaffolding arrangement. Individuals alone take risks simply by climbing up the scaffold tower to where they need to work, if they should carry up supplies and tools too then the chance of accidents considerably increases; this is where the use of a scaffold hoist comes in, placed Wherever you need it, the hoist will take up all your equipment and supplies at the touch of a button, this technique is not just a great deal quicker but more significantly a great deal safer.
The accessories that are available to be used with the scaffold hoist offer huge benefits. They permit particular items to be lifted with the hoist to wherever required; the accessories consist of buckets for mortar, chutes to carry waste to a skip at ground level, chains to lift a loaded wheelbarrow in its entirety as well as chains for lifting smaller skips.
A scaffold hoist's cost effectiveness is a significant advantage, now we'll consider how.
Numerous construction businesses quote jobs depending on the time it's going to take, longer builds usually cost more. Because a scaffold hoist is electrically driven it will lift up and lower loads pretty quick, as compared to a human carrying objects unsteadily up and down a dangerous scaffold tower. Time off for accidents and injuries are common, frequently caused by lifting heavy loads, more so when awkwardly carrying them up a scaffold; Back and knee injuries are renowned amongst builders, yet the stress on the human skeleton may be minimised by the use of a builder's scaffold hoist, therefore resulting in less time off work for injuries, no reduction in manpower and consequently no time lost on the job.
Does Your Contracting Company Suffer From a Hidden Problem?
Millions of contractors share a problem. It's so common that many contractors feel that they just have to live with it and no longer even think about it. So, it hides in the shadows of their business preventing them from making a good profit.
What is this problem? NOT ENOUGH CUSTOMERS.
How do I know this? I've been a contractor in Los Angeles since 1979, for over 30 years. We've been through several recessions where some of my competitors have gone belly up. I'm not saying that my business has always thrived, but it's survived. For me, the saving grace that has allowed me to build a 25-person electrical contracting company has been having enough customers.
If you're a contractor, let me ask you: What would happen if you had two or three times as many customers waiting for bids? Wouldn't you bid your jobs higher, sell more jobs, and make more profit? For most contractors, the answer is yes. But why is the answer yes? After all, contractors need to do a lot of things right to make a profit, not just find customers.
There are a lot of steps in contracting -- and a lot of things that can go wrong. From the moment a customer first calls you to the moment you're paid in full on a completed job, you must handle each step and many details skillfully. You must bid the job, sell the job, schedule the work, purchase material, organize all the aspects of the work, complete each aspect satisfactorily, and finally, get paid.
Fortunately, most contractors do well enough at these steps that if they could just get enough customers, they could take it from there and make a fine profit. The one thing most contractors agree they have a problem with is not enough customers.
Getting customers is done in two steps. The first is promotion. Promotion is getting the word out so that you get calls or e-mails from customers. Contractors have typically done this with Yellow Pages, flyers, telemarketing, and even radio and TV ads. Today, of course, a lot of promotion is done on the Internet. When Internet promotion is done properly a contractor can expect a large percentage of qualified customers looking for their specific services to find the contractor's website and then call or e-mails them.
Once your promotion has gotten the customer to call, the second step is sales -- bidding the job and selling the customer on your doing the job
Things to Watch Out for in a Modular Office Building
Modular office systems actually are used for numerous purposes which range from guard shacks to long term in-plant office buildings. You simply can not overcome the flexibility of these prefabricated office buildings. So for starters, you will be able to count on no messy cleanup of construction waste materials once the structure is assembled and if you want to move the structure at some point, that much simpler also.
So what exactly are prefabricated office systems?
Having the ability to bolt these types of buildings together from prefabricated panels is their real secret. The prefabricated wall panels are bolted together with a metal stud technique that defines the constructs fundamental layout.
You ought to talk over with your distributor what wall finishes are most appropriate for your situation. This will likely be included while in the development phase. They also run in a variety of sizes to simplify construction and give more design flexibility.
Don't forget to consider options...
It truly is your options that make modular offices quite popular. The options help them adapt to any kind of circumstance. While steel doors are common selections, frequently people choose the solid wood doors if provided with the option. Windows in doors are normally a great option and therefore are usually high on the checklist of features people would like.
Another primary option you'll want to take into consideration is windows. Which windows, if any, has to be operable is one more thing to consider. Don't forget to take into account the benefit of full height glass panels when planning your office space. Your manufacturer could possibly make suggestions.
Electrical raceways built into the structure is yet another solution you might like to take into account given that they can be entered from inside and outside the structure.
So what type of rewards will modular engineering present?
There are few features greater than having the ability to dismantle a structure with ordinary tools and move it to a new area easily and quickly. What's more, because of its hassle-free bolt together system, it can be easily altered when you need more room or need to allow for layout modifications
Form Protection Coating
In the prestress/precast concrete industry, a critical component to the manufacturing process is the form (mold). Forms give the concrete components their unique shapes and they help hold the internal reinforcing in place. Depending on the type of concrete structure being built, some forms can cost well over $100, 000.00 and require hundreds of man hours to set up and erect.
With all that money invested in forms, there is one little thing that can turn your investment into scrap metal and that is rust!
In order for your finished concrete components to look smooth, unblemished and professional, the forms have to have smooth, undamaged contact surfaces. With moisture, rain and salt air, if your steel forms are left unprotected, they will start to rust and pit making your forms unusable and resulting in thousands of dollars that will have to be spent in labor to grind and smooth the form surfaces. In some cases, the forms have to be scrapped altogether.
PSI Form Protection Coating is a valuable tool to protect your forms while not in use. Application is easy. Using a mop, apply one coat. Wait for it to dry and then apply a second coat. This will protect your form for short or long term storage. When you are ready to start using your form again, just spray the coated surface down with mineral spirits and let it activate for a few minutes. Wipe off the coating and you are ready to pour.
If you have a steel form you are about to store, try some of the PSI Form Protection Coating and you will be convinced that this is the only way to store your forms.
How It Works
PSI Form Protection Coating works hard to protect your precious forms by creating a dual-action film on the surface of any form that will double as a weather protecting agent. It contains a high molecular weight, with non-reactive, chemically inert ingredients that combine to form a highly protective layer to protect forms made out of any material from damage during storage, both inside and out.
It is so safe to use that it can be used on both forms and other equipment for both protection and easy cleaning, as often as needed. It can be applied to both pre-stressed and pre-cast forms, and will not stain or discolor concrete during use. It produces cleaner casts, increases the life of wood forms, and prevents rust and corrosion from building up on metal forms.
Subscribe to:
Posts (Atom)